Investment in technology for rapid, accurate planning: efficiently and cost-effectively housing cows and storing slurry
Wolfenden’s highly-skilled specialist staff are using the latest software to respond quickly and accurately to dairy farmers’ building and slurry requirements, and there is clear communication at all stages with everyone involved in the project – meaning no nasty surprises or costly oversights along the way.
With decades of experience working with dairy farmers, Wolfenden have always understood the constraints of time – herd housing and slurry management can’t be delayed by build issues – and cost, no more so than in the current economic and political climate. Wolfenden’s proactive approach and the company’s significant investment in growth and innovation – including developing new products specifically for the dairy sector, such as the SUPA range – make them the supplier of choice for dairy projects across the UK.
One areas where Wolfenden have invested to help both farmers and engineers with the building process is in their use of 3D modelling technology and in ERP / CRM, to help ensure a smooth workflow from initial enquiry through to project completion.
Wolfenden use Tekla 3D modelling software – the architectural modelling tool used by some of the world’s largest structural engineering firms and precast concrete specialists. In standard use, the software has a range of benefits, from estimating and bidding through to detailing, fabrication, and planning and coordination. However, putting dairy farmers at the centre of the design and manufacturing processes, Wolfenden have adapted their use of Tekla to suit the very specific needs of their customers. Jade Moody, CAD technician at Wolfenden explains,
“In its straightforward use, everything for a 3D model will already be in a supplier’s catalogue and you can just drag and drop products into the model – down to the nuts and bolts of a job – and then adjust the sizes accordingly. For Wolfenden, a lot of our components are bespoke – no two farms are the same, after all. I draw them in detail, to size and with reinforcing built in, so that the 3D model represents an exact replica of the farm once the project is completed.”
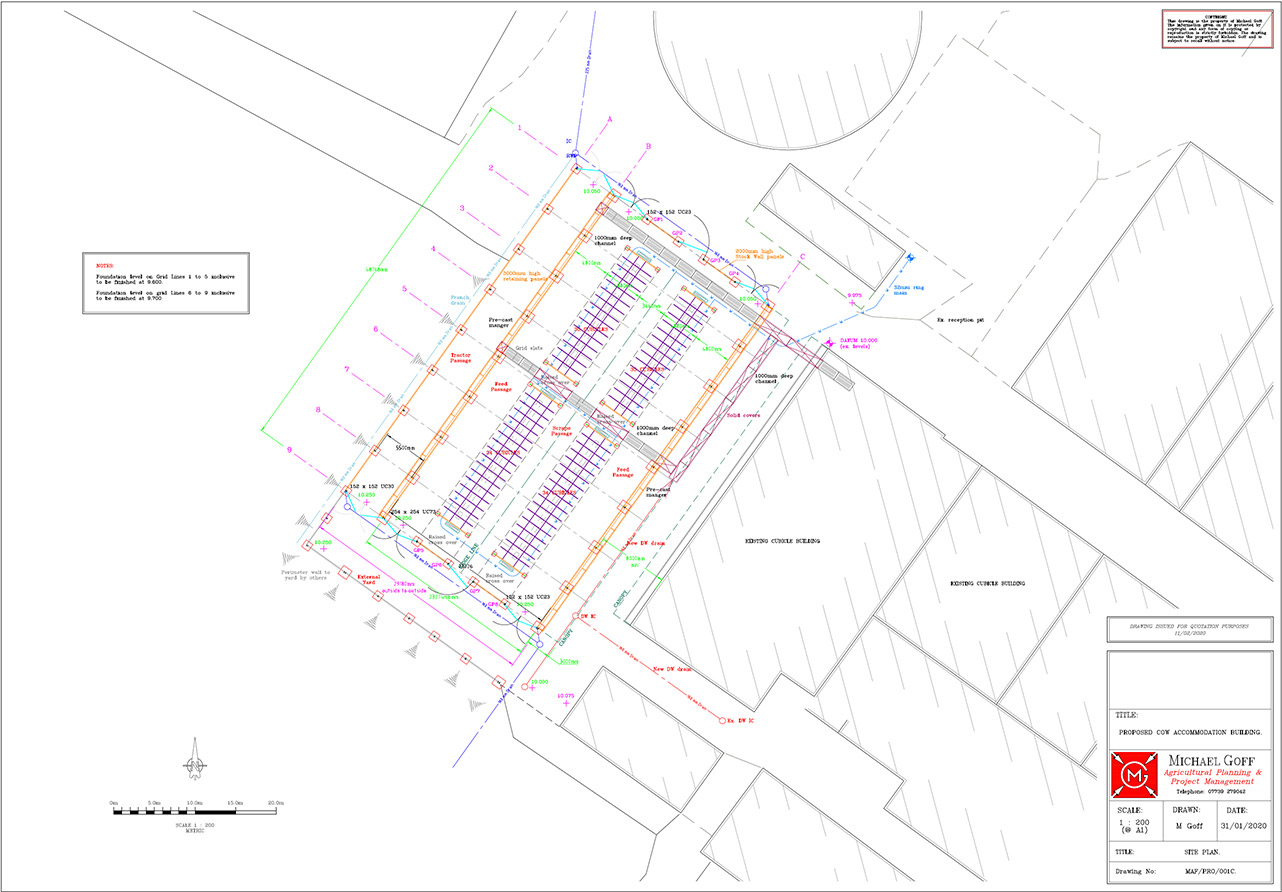
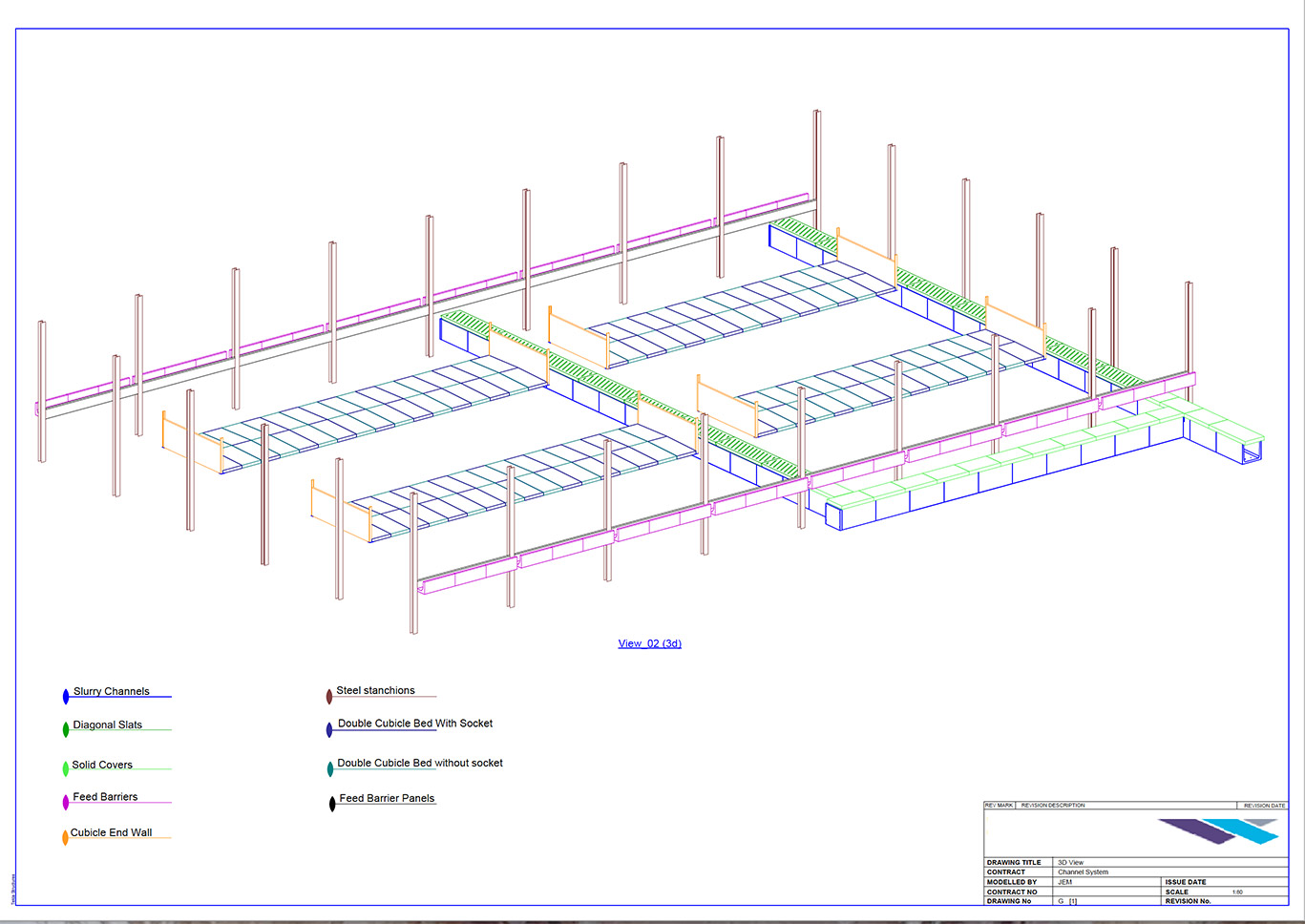
The process of getting raw data into a 3D model varies, depending on what information is available and how this is presented, and Wolfenden are flexible in the ways they work with farmers and engineers to create an accurate 3D model, one that can be adapted to any changing requirements throughout the duration of the build. For example, sometimes a farmer or project engineer will have an architectural drawing which is a 2D visualisation of the overall layout of the building. Wolfenden can use this to work out the necessary products – whether in stock or bespoke – and then create the 3D model which can be shared with everyone involved in the build (images 1 and 2 show the architects plan converted to a 3D view). Alternatively, in the design of new slurry facilities for example, a farmer may specify the size of tank and what passageways and space they want for the tank layout and then Wolfenden will work out the best way to meet their requirements, specifying the most appropriate products in the most cost-effective and efficient way.
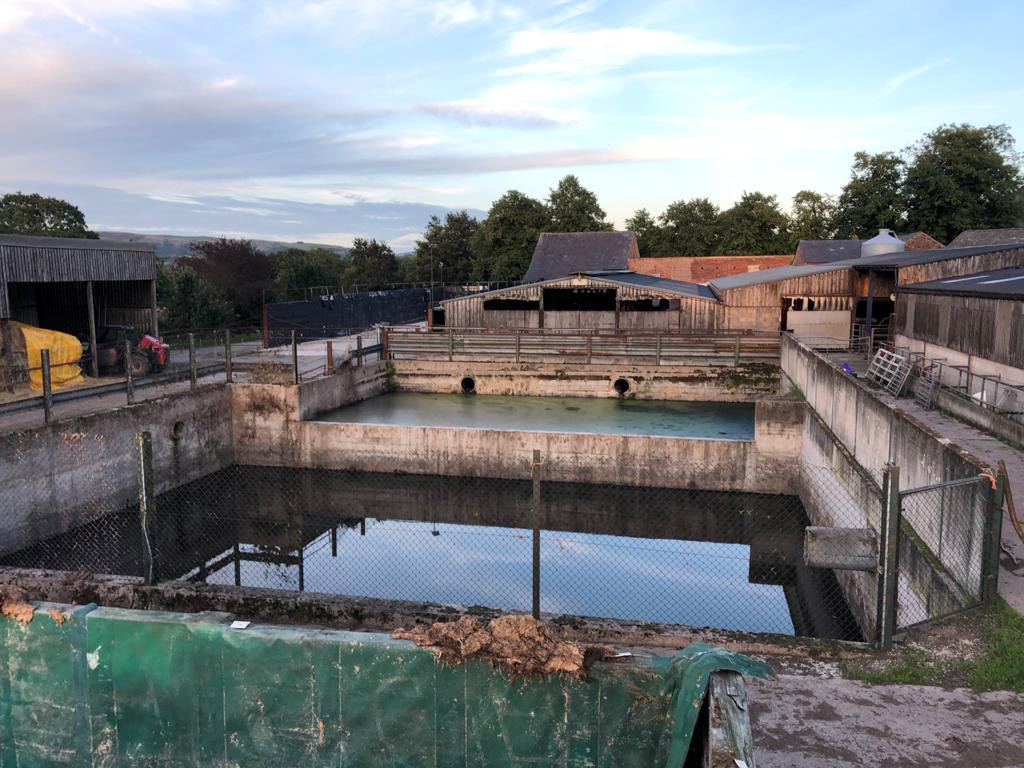
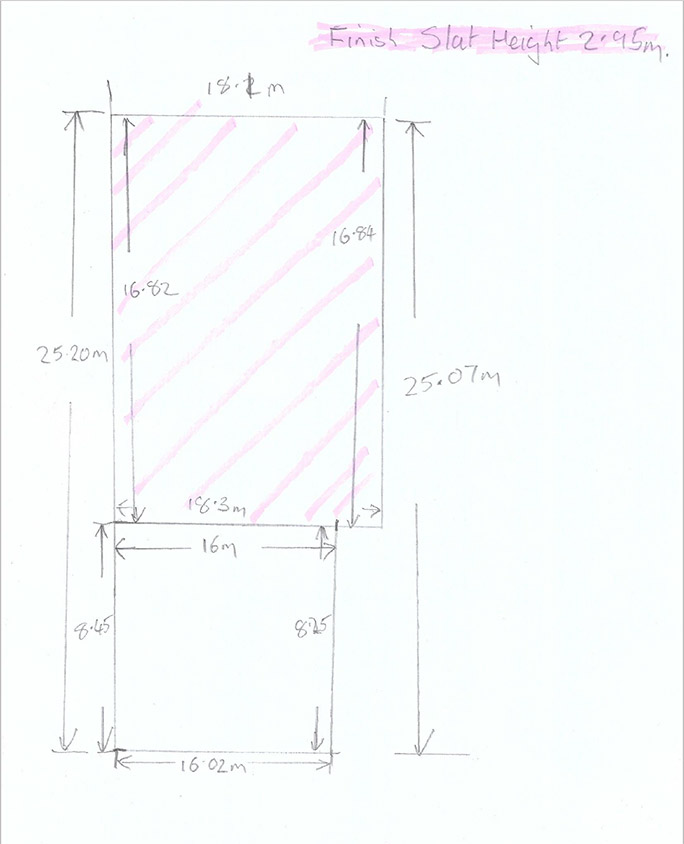
Sometimes, a customer will have a rough sketch of their idea, with guideline sizing indications (images 3 and 4 shows one customer’s site before work and their sketch of dimensions provided to Wolfenden). Wolfenden will use this as the starting point, in consultation with the customer, to create the full 3D model and incorporate product requirements which are then transparent and easily communicated (images 5 and 6 show the slurry project overview and 3D model for this project). Farmers will often rely on Wolfenden’s expertise and advice, in terms of build requirements, focusing instead on how many cows they want to house and how often they’ll want to clean out the finished build. In this scenario, Wolfenden consult the relevant standards, calculate how many gallons of storage are required and then design and construct the model once these elements are factored in.
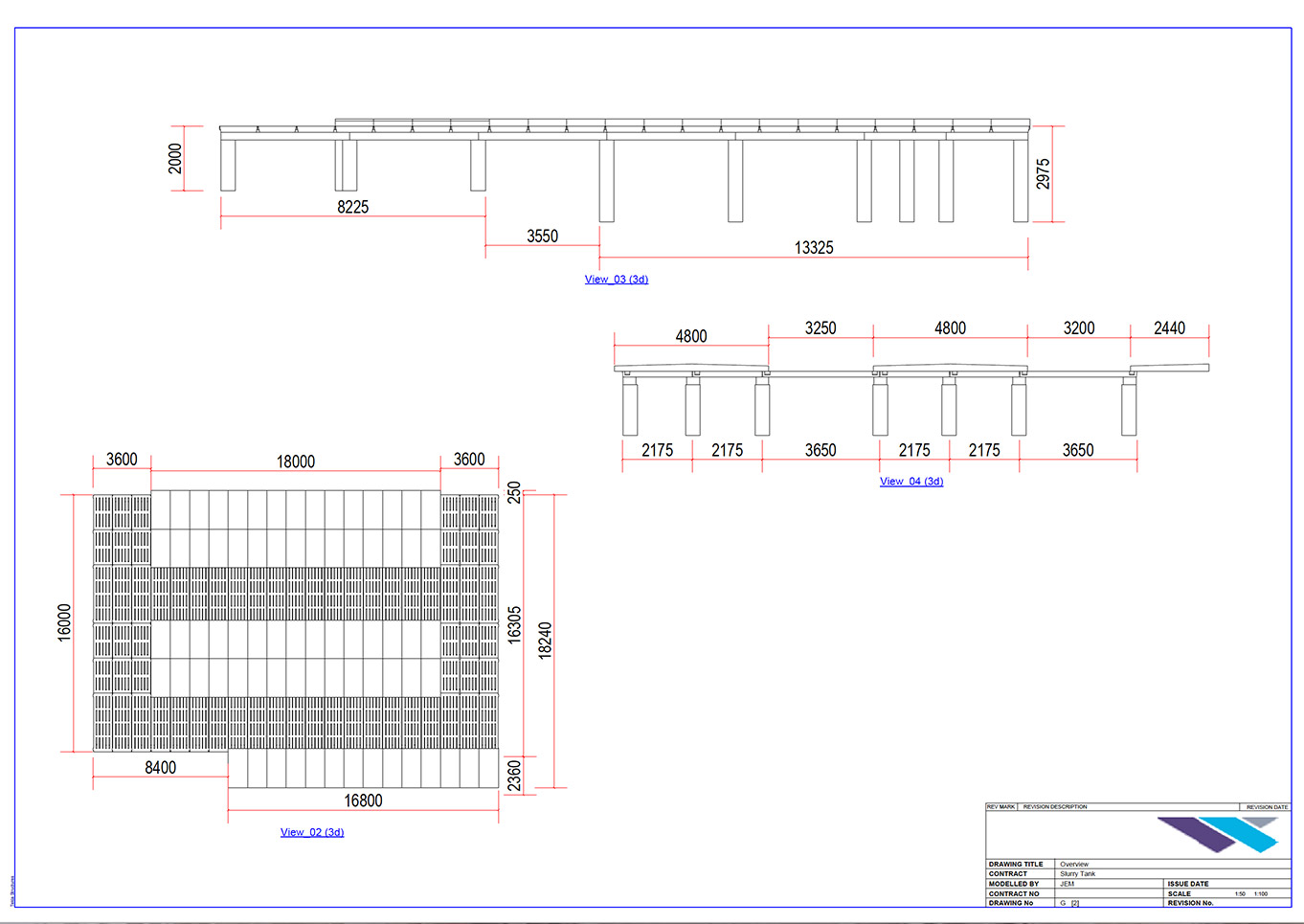
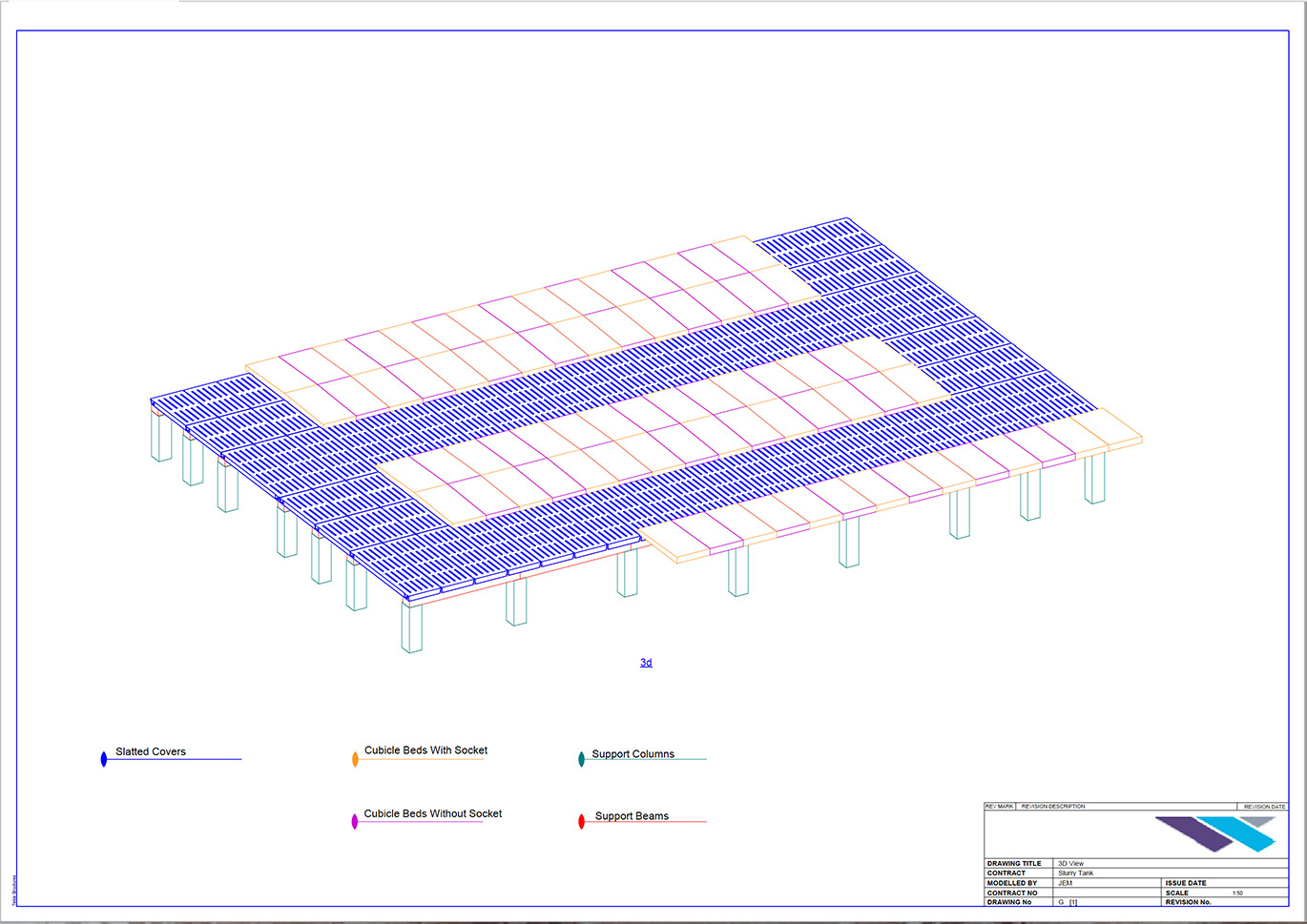
Whatever the starting point and initial information, once all the requirements have been modelled Wolfenden maintain clear communication with the customer and with contractors involved in the project. Having a 3D model rather than flat drawings makes it easier to visualise the final building for all parties, and farmers can see more clearly what they are getting for their money. Clashes are more easily spotted in 3D, for example where initial angles and joints won’t work in the real landscape, which may be at a different gradient than first visualised. Addressing such issues at the modelling stage has clear benefits, reducing material wastage, meaning the right products are specified prior to manufacture and work on-site can run more smoothly with fewer costly unplanned stoppages.
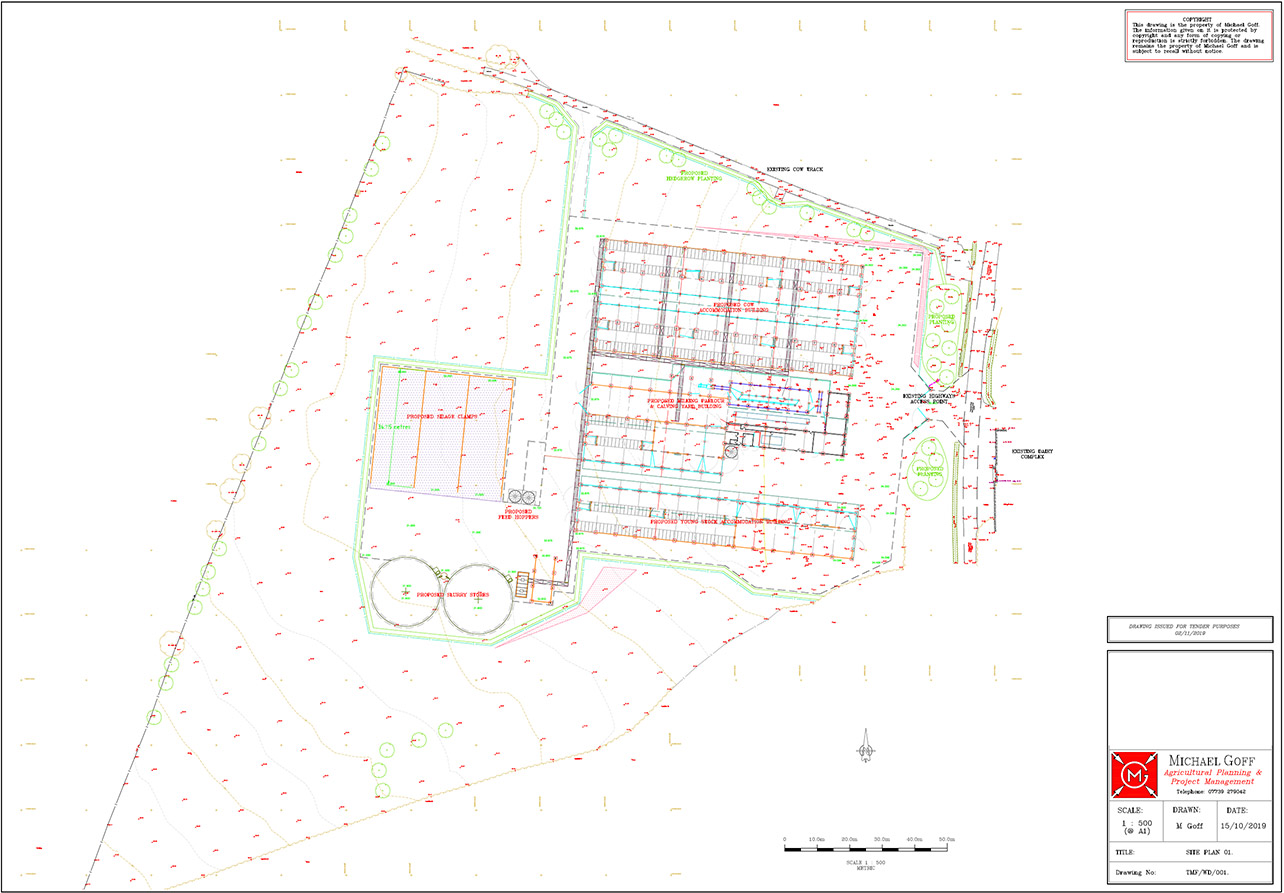
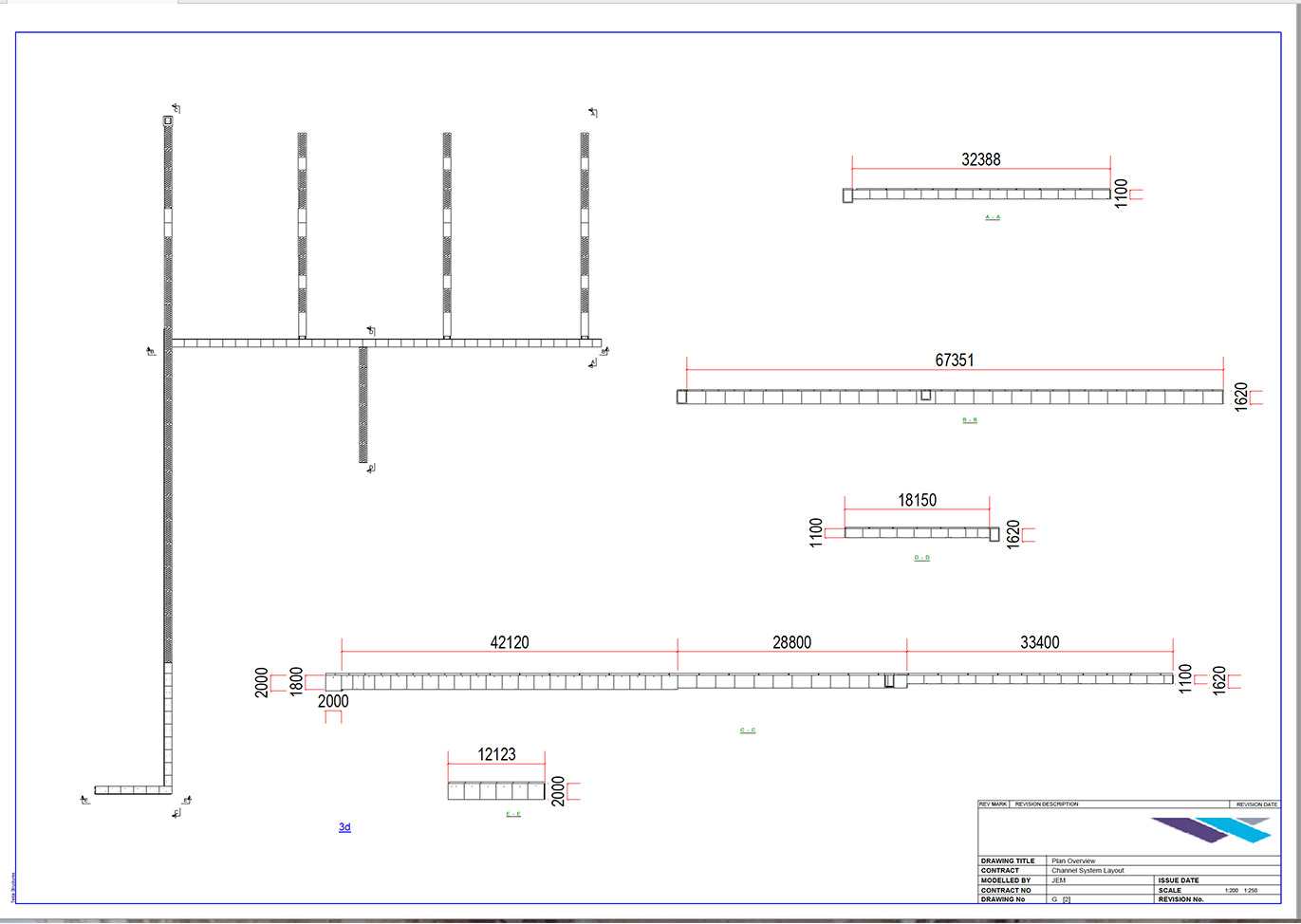
Once approved, Wolfenden convert the model into product drawings, to calculate the required amounts of all components and products, speeding up the costing on the job and saving time in preparing for work on-site. Everyone involved in the project can see the intentions and details of the design and having the drawings available to all parties, all the time, improves collaboration and communication between customer, from manufacture to site work. And, for contractors, working with Wolfenden can make it easier to win contracts. For one recent project, the main contractor bidding for the overall project relied heavily on Wolfenden’s CAD – with the drawings re-worked several times prior to finalising the tender – to accurately cost and successfully compete for the project (as shown in image 7 – the architects’ drawing, image 8 – Wolfenden’s CAD overview and image 9 – the 3D view). Jade continues,
“One of the real benefits of using Tekla is that I can change things around on a job and adapt already-working jobs as sizes sometimes change with the site coming together during the building stage. The drawings can always be kept up-to-date so that there’s no confusion between different contractors, the customer and ourselves, and we can adapt our manufacturing requirements which can cut down the lead time on getting products on-site when they’re needed.”
Image 9
To ensure the most efficient and cost-effective manufacturing and planning processes, Wolfenden have made significant investment in a new ERP / CRM system which will run in the background and flag up purchasing needs, such as requirements for steel for forthcoming builds, to help minimise delay in the manufacturing, delivery and installation on farm builds. And, during the actual build, Wolfenden’s investment in Tekla and their expert staff are on hand to help make contractors’ work that much easier. Jade, again,
“In terms of detailing, I’ll often do numerous drawings of a job, to help show the full layout. I’ve often done a separate layout of the beams and columns of a large tank to ensure that these are laid out correctly, on-site. We are continually expanding what we do with the 3D modelling, both on the building and on the technical side, so that we can use our resources to further help farmers and engineers from the design stage through to completion so that everything we do at Wolfenden contributes to a cost-effective, well-designed and snag-free build.”
Saving time and money and making communication and collaboration easier between farmers and building contractors, Wolfenden’s investment in world-class modelling software and their adaptation of the workflow to suit the specific sector demands offers a clear commitment to the needs of dairy farmers and agricultural building designers, alike.